Understanding bar grating weight is crucial for those involved in industries where safety, durability, and efficiency are key. Bar grating, a versatile and trusted flooring and structural material, is utilized in a range of applications, from industrial platforms to catwalks. A comprehensive grasp of the weight factors of bar grating not only ensures optimal design and functionality but also enhances trust in your infrastructure projects by adhering to safety standards and facilitating load management.
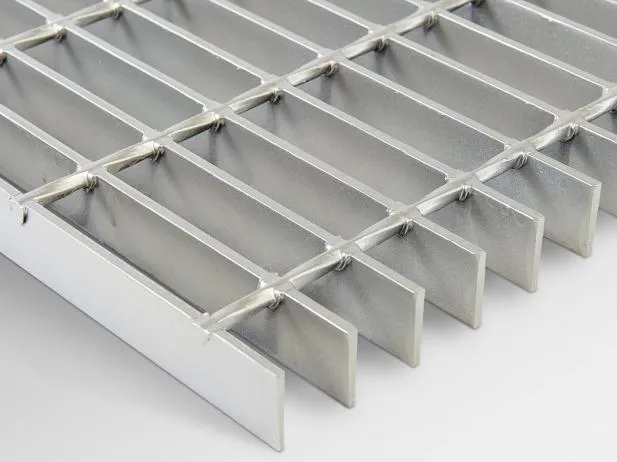
Bar grating weight is determined by several factors, including the material used, the size of the bars, and the spacing between them. The weight of bar grating directly influences the ease of installation, cost, and overall functionality of a project. Typically, bar grating is manufactured using materials such as aluminum, steel, and stainless steel, each offering unique benefits and weight characteristics.
Steel bar grating is the most common type used across industries due to its exceptional strength and durability. However, the weight of steel bar grating is substantially higher than its aluminum counterpart. For instance, a standard steel bar grating panel may weigh around 17 lbs per square foot, making it ideal for surfaces that require additional strength and load-bearing capacity. This high weight not only guarantees stability but also extends the lifespan of the installation in heavy-duty environments.
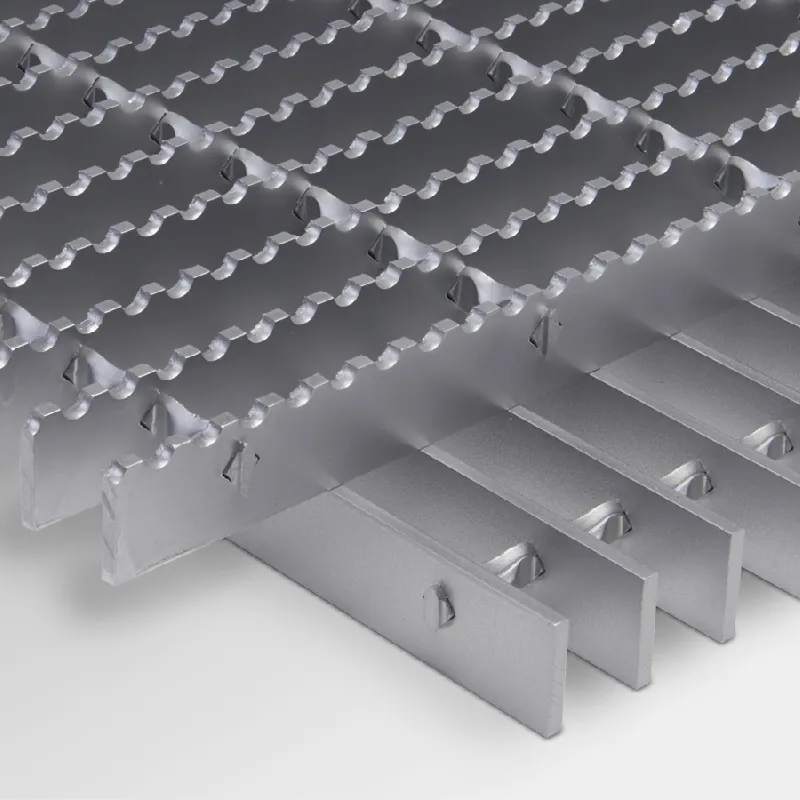
Conversely,
aluminum bar grating is preferred in projects where weight is a significant concern. Weighing approximately one-third of steel, aluminum grating is suitable for applications where ease of transport and installation is a priority without compromising on safety and reliability. It is specifically advantageous in scenarios where frequent installation and removable access are required. Aluminum's resistance to corrosion also makes it ideal for environments exposed to moisture and chemical exposure.
Stainless steel grating, though heavier than aluminum, offers a middle ground with enhanced resistance to corrosion compared to regular steel. Its unique equilibrium of strength, aesthetics, and corrosion resistance makes it suitable for industrial and architectural applications where a sleek, long-lasting finish is essential.
bar grating weight
Beyond material, the size and configuration of the bars in the grating also significantly impact its weight. Bar grating can be customized in a variety of dimensions, each suited to different load requirements and aesthetic considerations. The width and thickness of the bars contribute to the overall weight, with thicker bars increasing the load capacity and the weight of the grating. The spacing between the bars also plays a critical role; closer spacing results in a denser and therefore heavier product.
Additionally, the manufacturing process, whether welded, swage-locked, or press-locked, influences the structural integrity and weight distribution of the grating. For example, welded grating, known for its robust construction, can be heavier due to the nature of the welding process which uses thick, steel bars fused together, offering unparalleled durability for demanding environments.
Understanding bar grating weight is essential in ensuring compliance with load restrictions and safety protocols, particularly in pedestrian traffic and vehicular areas. Experts recommend conducting a thorough load analysis and consulting with a bar grating supplier experienced in the specific industry application to ensure that the chosen material and design meet the regulatory requirements and project specifications.
In conclusion, selecting the appropriate bar grating weight hinges on a meticulous evaluation of the project needs, including load-bearing requirements, environmental factors, and aesthetic considerations. Professionals in engineering and architecture should collaborate closely with reputable manufacturers and suppliers, who can provide authoritative information about their products. By leveraging experienced insights and adhering to industry standards, projects utilizing bar grating can achieve a balance between performance, safety, and cost-efficiency, ensuring resilient and reliable installations.