Steel grating has become a quintessential component across various industries, serving applications that demand strength, durability, and versatility. As industries continue to evolve, understanding the intricate details of steel grating specifications becomes integral for optimal utilization. Leveraging authentic experiences and accrued expertise, this article unravels the complex world of steel grating, ensuring authoritative insights that build trust.
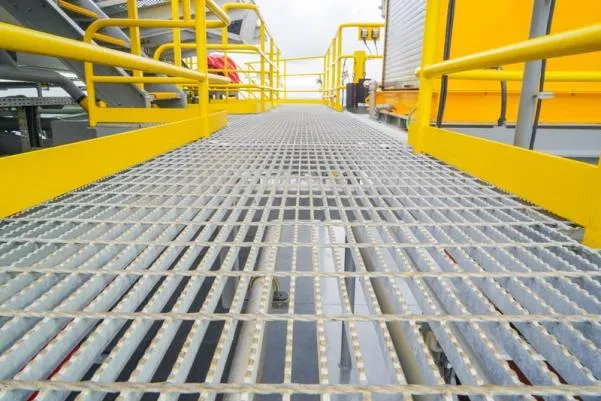
Steel grating is predominantly constructed from carbon steel, stainless steel, or aluminum, each material offering unique benefits. Carbon steel gratings are renowned for their cost-effectiveness and high strength. These gratings undergo galvanization to enhance corrosion resistance. Stainless steel gratings are preferred in environments exposed to corrosive elements, ensuring longevity and easy maintenance. Aluminum gratings, known for their lightweight and corrosion resistance, are ideal for applications demanding ease of installation and manipulation.
When detailing specifications, one cannot overlook the load-bearing capacity, which is a critical parameter.
The load grating can bear depends significantly on the bar size and spacing. For industrial applications, common bar sizes range from 3/16 to 1, with spacing options such as 19W4 or 30W4—these designations describe the pitch of the bearing bars and the size of the openings. A 19W4 spacing, for instance, signifies 1-3/16 between the bearing bars and 4 between cross bars, optimizing the grating for specific weight distribution demands.
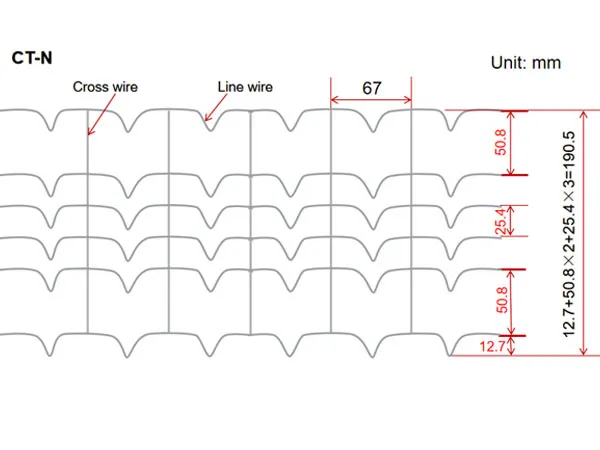
Another pivotal aspect is the grating type. Welded steel grating, composed of a series of parallel bearing bars joined by cross bars, is widely utilized due to its robust durability and robust weight support. Press-locked gratings offer a sleek appearance and are frequently chosen for architectural applications. Meanwhile, riveted grating provides superior load-bearing capacity, ideal for achieving maximum strength.
While specifying steel grating, surface treatment is a crucial element that augments both aesthetic and functional attributes. Galvanized finishes prevent rust, vital for outdoor installations. Painted finishes or powder coatings can offer visual appeal and extra protective layers to prolong the grating's lifespan. In environments that prioritize slip resistance, serrated grating surfaces are recommended, reducing the risk of accidents and ensuring workplace safety.
steel grating specifications
Installation considerations further demonstrate the breadth of knowledge required to effectively use steel grating. Proper securing to the framework is vital for stability, involving welding or the use of saddle clips, depending on the application requirements. This procedure necessitates an appreciation for environmental conditions and the expected foot or vehicular traffic.
The sustainability aspect of steel grating also garners attention, especially as industries aim to lower environmental footprints. Recyclability stands out; steel grating's material composition allows it to be repurposed efficiently, minimizing waste and aligning with green building initiatives. Selecting materials that undergo environmentally friendly production processes can further enhance eco-credentials, demonstrating a commitment to sustainable practice.
In a landscape of ever-evolving industrial standards, emerging technologies aim to innovate steel grating use. 3D modeling and simulation ensure precise specification adherence, optimizing material use and preemptively identifying potential design flaws. These technological advancements assist engineers and architects in creating safer, more efficient solutions.
Throughout the decision-making process, it is vital to engage with stakeholders who demonstrate expertise and uphold industry standards. Reputable suppliers offer invaluable insight, assuring that the steel grating meets stringent industry criteria—thus reinforcing trust and accountability.
Ultimately, steel grating specifications encompass a multitude of considerations, each influencing performance and efficiency. Drawing upon authentic expertise ensures that these components not only meet but exceed application demands, setting benchmarks for quality and reliability. With continued dedication to innovation and adherence to industry standards, steel grating remains a steadfast ally across myriad applications. Embracing expert knowledge solidifies its role in fortifying infrastructures worldwide.