Understanding the Costs of Steel Grating Factors and Insights
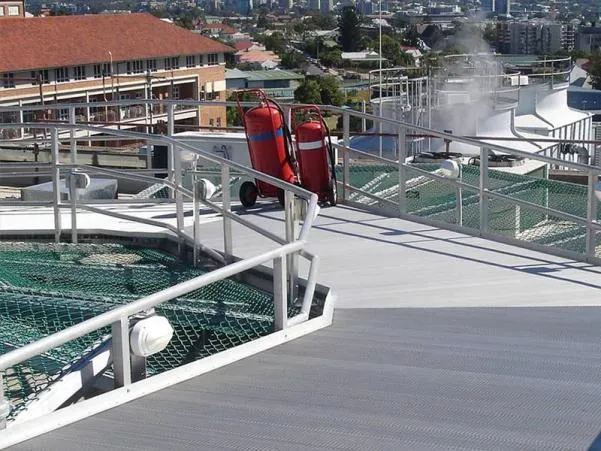
Steel grating plays a crucial role in various industries due to its strength, durability, and versatility. From construction and manufacturing to oil and gas projects, its applications are extensive. However, understanding the costs associated with steel grating can be complex, involving numerous factors that potential buyers need to consider. This article aims to provide an authoritative insight into what influences the cost of steel grating, thereby empowering decision-makers with the expertise needed to make informed purchasing decisions.
One of the primary factors influencing the cost of steel grating is the type of material used. Steel gratings are typically made from carbon steel, stainless steel, or aluminum. Carbon steel is widely used due to its affordability and adequate strength properties. Stainless steel, while more expensive, offers superior corrosion resistance, making it ideal for harsh environments. Aluminum gratings, though the costliest, offer excellent resistance to corrosion and are significantly lighter, benefiting projects where weight is a concern.
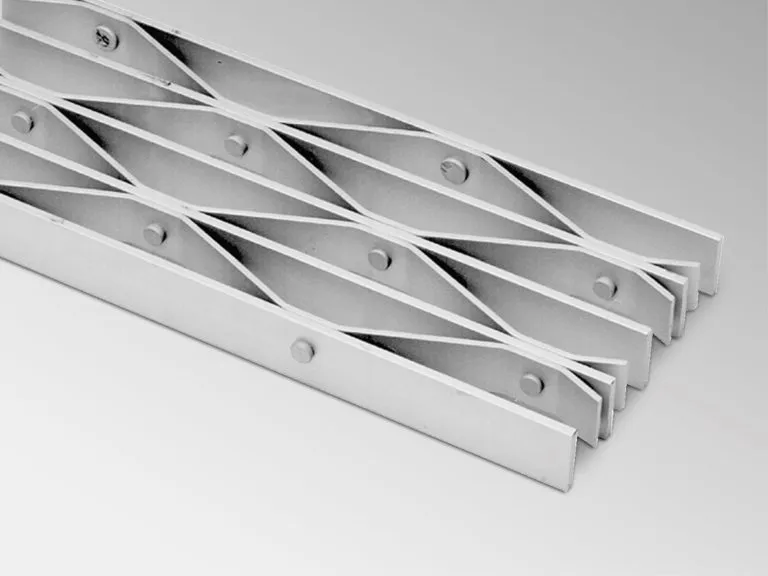
The manufacturing process further affects the cost.
Pressure-locked gratings tend to be pricier than welded options. Pressure-locked types provide an aesthetically pleasing finish and tight tolerances, suitable for architectural applications. Conversely, welded gratings, known for their robustness, are favored in industrial settings where strength and durability are paramount, resulting in a cost-effective choice for those applications.
Size and dimensions of the grating panels also play a significant role. Larger panels require more material and can increase shipping costs, impacting the final price. The thickness of the bars and the spacing between them are crucial — wider spacing may reduce costs due to less material use, but it could also mean sacrificing strength depending on the load requirements. Professionals must assess these specifications according to the specific load-bearing requirements of their projects to avoid unnecessary expenditures while ensuring safety and performance.
steel grating cost
Additionally, customization can lead to increased costs. When projects demand unique sizes, shapes, or finishes, the customization required can lead to higher fabrication costs. Companies often charge extra for custom-cutting, specialized coatings, or treatments such as galvanizing for enhanced corrosion resistance. Thus, while customization allows for more precise project needs to be met, it is essential to balance these requirements against budget constraints.
The geographic location of suppliers can influence pricing through both material availability and logistical costs. Purchasing from local suppliers might reduce transportation expenses and delivery times, while importing materials could incur higher costs due to tariffs and shipping charges. Furthermore, regional economic factors can also impact pricing, making it vital for buyers to evaluate the trade-offs between local availability and sourcing from manufacturers with lower baseline prices.
Market conditions fluctuate, affecting the raw material prices. The global steel market impacts the cost of steel grating significantly. When steel prices rise due to increased demand or supply chain disruptions, the cost of grating products often follows suit. Staying informed about market trends allows businesses to forecast price changes and optimize purchasing strategies accordingly.
Finally, the choice of supplier can determine not just cost, but the reliability and quality of the product as well. Suppliers with established reputations in the industry provide assurance of quality and compliance with standards, which is crucial for maintaining trustworthiness. It is advisable to seek out suppliers who offer a balance of cost-competitiveness and proven track records in delivering durable, high-quality grating products.
In conclusion, the cost of steel grating is not governed solely by material expenses; rather, it is a sum of material type, manufacturing process, size dimensions, customization, supplier location, market conditions, and supplier reliability. A thorough evaluation of each factor ensures that buyers achieve the most value for their investments, ensuring efficiency, safety, and durability in their projects. By selecting steel grating that aligns with project requirements and budgetary constraints, businesses can optimize performance while maintaining cost-effectiveness, thereby staying competitive and proactive in their respective industries.