Shaker screens are an integral part of the mining and oil industries, where their main function is to separate particles of different sizes during the sifting process. With rapid advancements in technology, selecting the right shaker screen has become crucial for businesses aiming to improve their operational efficiency and output quality. This article delves into the nuances of shaker screens, combining in-depth analysis with real-life insights to elucidate their significance.
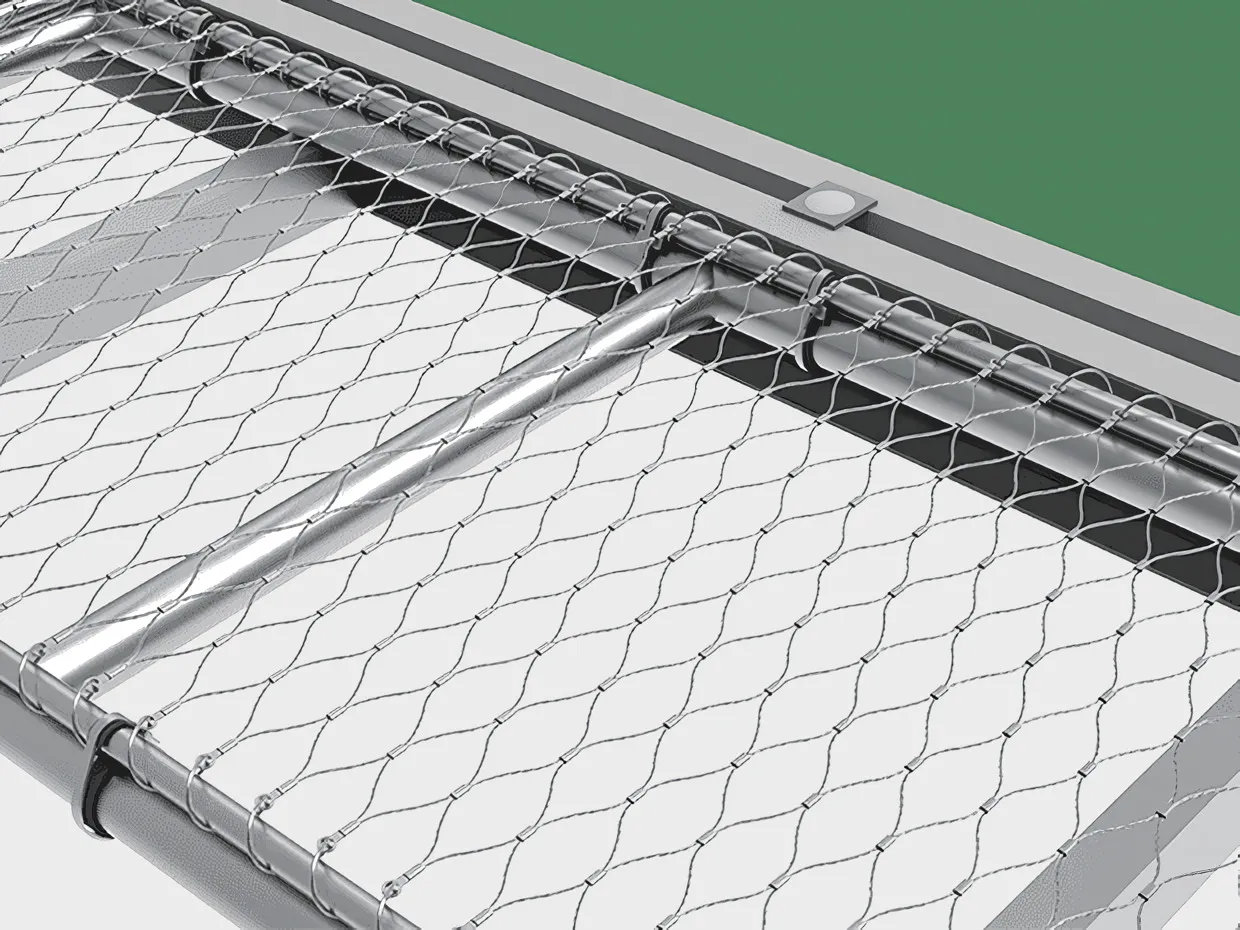
In recent years, the design and efficiency of shaker screens have undergone substantial enhancements, making them much more effective in their roles. Multi-layered shaker screens, for instance, now offer improved capacity and precision by combining various mesh designs. Such innovations have dramatically reduced the need for secondary handling of materials, thereby elevating operational reliability. The incorporation of newer materials like polyurethane and fine stainless steel mesh ensures prolonged durability and performance, even in harsh environmental conditions.
One key quality metric for shaker screens is mesh size, which dictates the particle size that can be filtered. Typically ranging from 20 to 400 mesh,
this measure determines the screen's effectiveness. Real-world assessments have confirmed that a nuanced approach to mesh selection can drastically impact the efficiency of material separation, directly correlating with the quality control practices of the facility utilizing these screens. Anecdotal experiences suggest that mismatched mesh sizes can lead to increased maintenance costs, downtime, and poorer product quality.
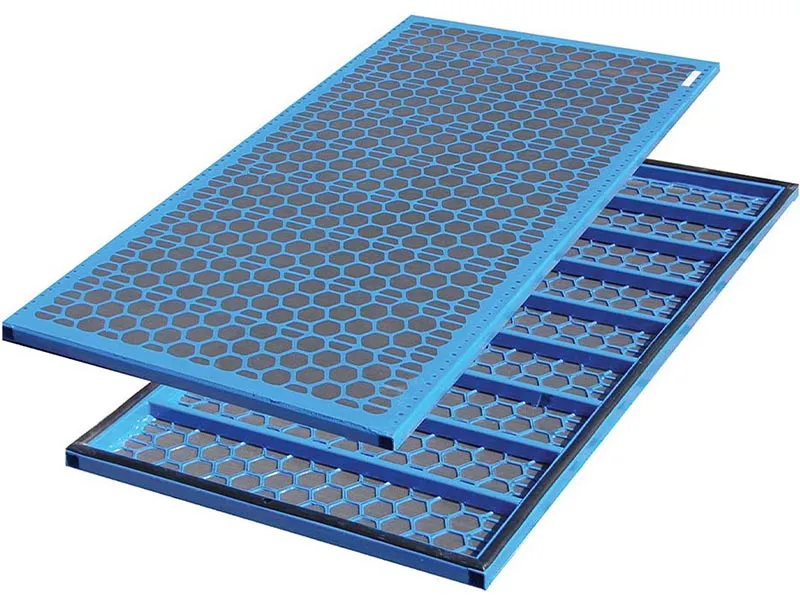
The expertise needed to select the most appropriate shaker screen extends beyond surface-level observations. Industry specialists underscore the importance of aligning screen choice with the specific requirements of the screened material. For example, operations dealing particularly with fine particles might favor screens with a higher mesh count, while coarser materials may benefit from screens with a wider aperture. A thorough understanding of material properties and the operational environment significantly influences this decision-making process.
shaker screens
Industry authority and credibility also hinge on the continuous testing and modification of shaker screen designs to meet evolving needs. Many leading manufacturers collaborate with field engineers and process managers to produce screens that cater to specific extraction processes. Such iterations involve rigorous lab testing followed by field deployment feedback cycles, thus enforcing a high standard of reliability and authoritativeness within the product offerings.
In building trust with clients and maintaining transparency, a growing trend among top brands is the provision of accessible technical support and customizable screen solutions. This customer-centric approach not only facilitates optimized product performance but also strengthens client relations, thereby consolidating the manufacturer's position as a trustworthy partner in operational success.
To sum up, the contemporary shaker screen stands as a product of exhaustive research, fine-tuning, and a granular understanding of industrial requirements. As technology marches forward and operational paradigms shift, investing in the right shaker screen entails a meticulous examination of mesh size, material properties, and vendor credibility. Businesses vested in mining and oil industries are thus urged to consider not only immediate cost but the long-term implications of their choice, prioritizing quality and reliability to sustain their competitive edge. As the landscape evolves, the trajectory of shaker screens will likely tilt further towards customization and enhanced functionality, solidifying their indispensable role across diverse operational settings.