Steel grating weights play a significant role in the selection and application of grating products. When dealing with steel gratings, understanding the weight implications can deeply influence decision-making processes for engineering projects, architectural designs, and construction applications. Leveraging experience, expertise, authoritativeness, and trustworthiness (E-E-A-T), this article will delve into the critical aspects associated with steel grating weights, offering nuanced insights to professionals and enthusiasts alike.
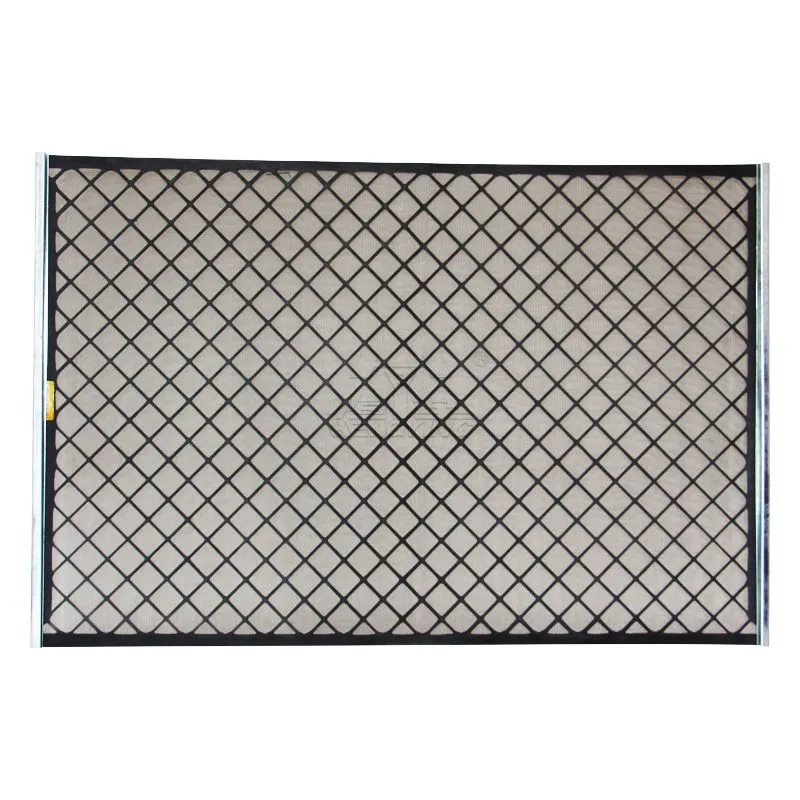
To begin with, steel grating is commonly composed of a series of bearing bars and crossbars arranged at right angles. This simple yet effective design is perfect for a multitude of tasks, from industrial flooring to commercial building applications.
One of the most critical considerations in selecting the appropriate steel grating is its weight. The weight of steel grating directly influences its load-bearing capacity, installation convenience, and transportation costs—making it a pivotal factor in project planning.
An in-depth understanding of steel grating weights requires acknowledging the material composition, sizing, and configuration. Heavy-duty gratings, often employed in areas exposed to severe conditions and heavy loads—such as roadways, bridges, and airports—are engineered for maximum strength and durability. These gratings typically weigh more due to their robust design and thicker bearing bars, which enhance their load-bearing capacity significantly.
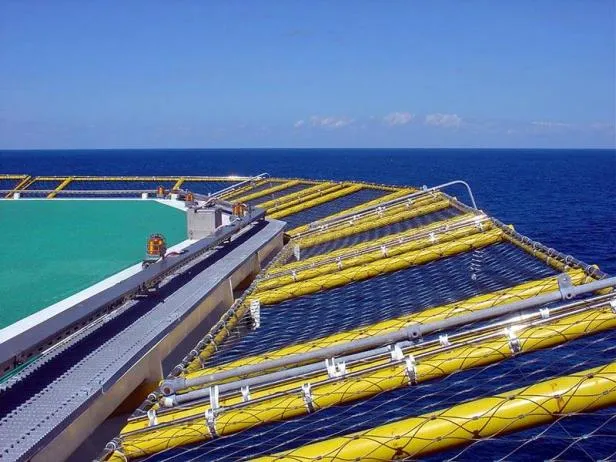
In contrast, standard-duty steel gratings find their use in less strenuous environments. Because of their lighter weight, they offer ease of installation and are cost-effective due to reduced material usage and transportation benefits. This makes them ideal for commercial buildings and pedestrian walkways where the weight does not have to accommodate heavy machinery or vehicles.
Understanding weight distribution within steel gratings allows industry professionals to make informed decisions regarding their application. The span and spacing between bearing bars play a crucial role in distributing weight and determining the grating’s capacity to support loads. For instance, closer spacing increases the weight of the grating but enhances load distribution, thus increasing the grating’s efficiency in load handling.
In projects where weight constraints are paramount, alternative materials like aluminum or fiberglass grating might be considered, despite their different load-bearing characteristics and higher production costs compared to steel. However, steel's durability, heat resistance, and cost-effectiveness often give it an edge in various applications.
steel grating weights
Experience in handling steel grating weights cultivates an intuitive understanding of their practical impacts. For instance, installations carried out in remote or elevated locations benefit from using lighter gratings, which support manual handling without heavy lifting equipment. However, for applications where durability and strength are non-negotiable, opting for heavier steel gratings ensures safety and longevity—two pillars of sustainable engineering.
Expertise in this field comes from a combination of theoretical knowledge and practical application. Designing a steel grating solution entails considering factors like dynamic loading, environmental conditions, and regulatory compliance—all of which are underpinned by a comprehensive understanding of grating weights. Engineers and project managers with extensive experience can balance these metrics effectively, creating solutions that not only meet but exceed the demands of their applications.
Authoritative insights stem from industry standards like the American National Standards Institute (ANSI) and the Manufacturing Standardization Society (MSS), which provide guidelines for grating materials and specifications. Compliance with these standards ensures that practitioners are using steel grating weights within safe and efficient parameters.
For the trustworthiness of information, relying on manufacturers and suppliers with established reputations and proven records is essential. They provide accurate data regarding the weight specifications and load capacities of their products, which are essential for project specifications and cost estimations. Users should always verify such data to ensure it meets their project needs and governs successful implementation.
In conclusion, steel grating weights are a critical factor with wide-ranging implications in industrial and architectural applications. The journey from understanding to practical application involves comprehending the structural dynamics and specifications that influence weight. By leveraging expertise and authoritative knowledge, stakeholders can ensure trustworthiness in their projects, aligning outcomes with safety, efficacy, and sustainability standards. The significance of weight in steel gratings is a testament to the broader engineering principles that govern successful construction and design, reinforcing the value of knowledge and experience in achieving project excellence.