Navigating the market for metal grating can drastically impact both budgetary considerations and project outcomes. Choosing the right type of metal grating and understanding the pricing dynamics not only optimizes costs but also enhances project quality and longevity.
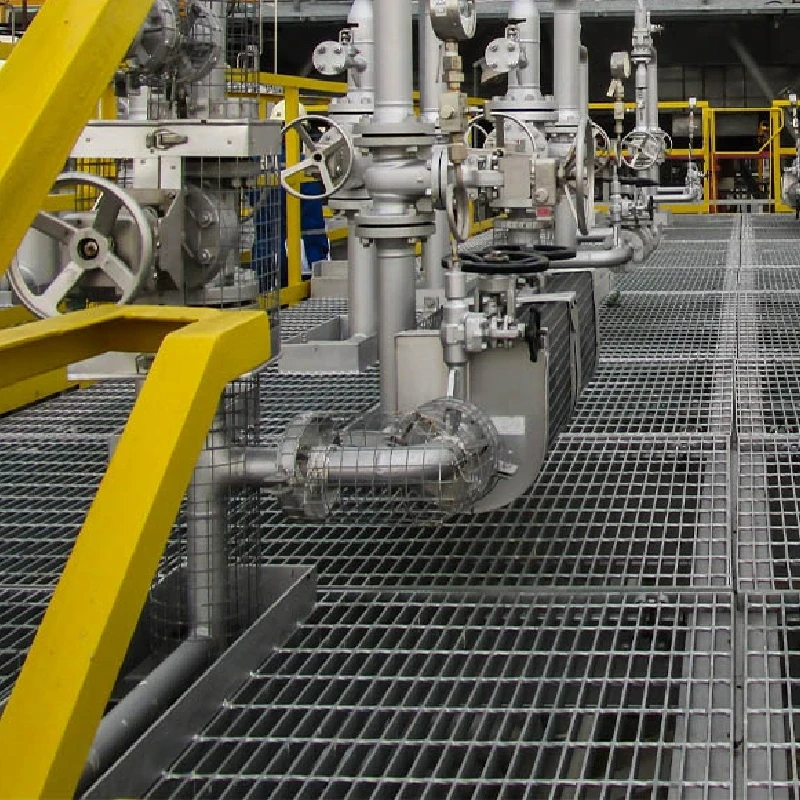
One of the foremost factors influencing metal grating price is the type of material used. Common options include steel, aluminum, and stainless steel. Each material offers unique benefits and cost implications. Steel is typically the most cost-effective option, prized for its durability and strength. However, its susceptibility to rust means it may require additional coatings or treatments, impacting overall expenses. On the other hand, stainless steel’s corrosion resistance and sleek appearance justify its higher price point, particularly for applications exposed to harsh environments or where aesthetics are a priority. Aluminum grating, while lightweight and corrosion-resistant, falls between these two in terms of pricing.
The manufacturing method also significantly affects cost. Press-locked, swaged, and welded gratings each have individual fabrication processes that contribute to their price variations. Welded gratings offer robust, long-lasting solutions and tend to be more affordable due to their lower manufacturing complexity. Conversely, swaged grating, which involves a meticulous interlocking process, often commands a premium due to the precision and labor involved.
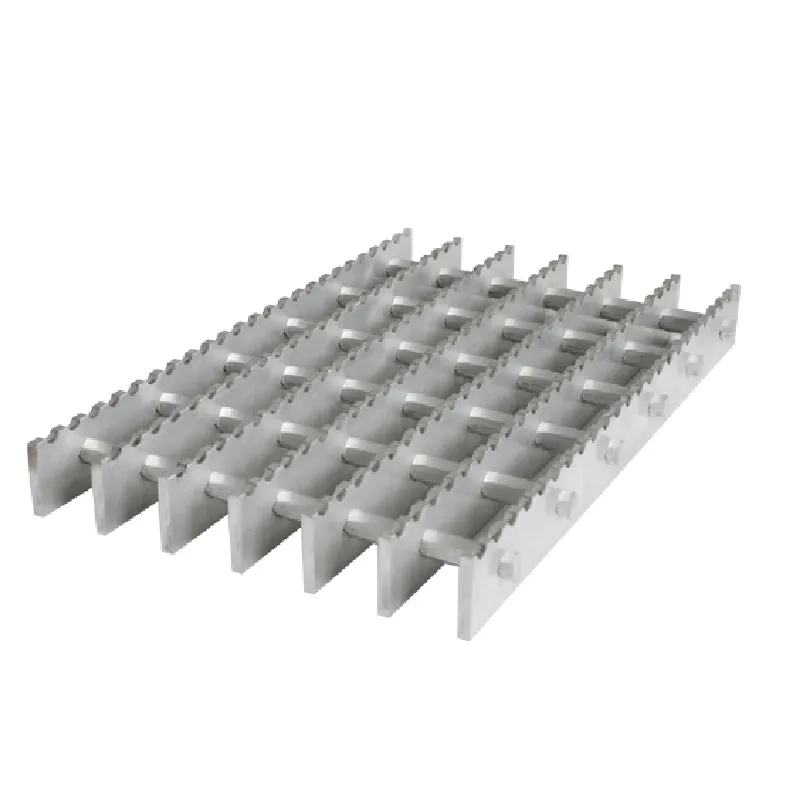
Load-bearing requirements further dictate pricing. Heavier loads necessitate thick bars and larger spacing, increasing both material and production costs. Engineers and procurement specialists should balance load capacity with budget constraints to prevent over-specification that may unnecessarily escalate costs.
Finishing options, such as galvanizing or powder coating, introduce another layer of price considerations. While these treatments add to the initial expense, they extend the grating's lifespan and minimize maintenance costs by safeguarding against the elements. For projects where longevity and low maintenance are critical, these finishing touches are often worth the additional investment.
metal grating price
Project location and associated transportation costs are often overlooked but influential in final pricing. Sourcing materials locally can significantly reduce shipping expenses, while international procurement might introduce tariffs and extended delivery timelines. Therefore, strategic sourcing can offer cost savings and smoother project execution.
Volume and lead time are additional levers in pricing. Bulk purchases frequently unlock discounts due to economies of scale. Long lead times provide manufacturers the flexibility to optimize production schedules, often leading to cost reductions. Thus, early and accurate project planning can leverage these factors to achieve more favorable pricing.
Real-life applications underscore the importance of aligning grating specifications with project needs. For instance, an infrastructure project in a coastal area prioritizing corrosion resistance may find greater value in stainless steel despite its higher cost. In contrast, an industrial warehouse might optimize costs with steel grating, investing in protective coatings to balance durability and budget.
In conclusion, understanding the interplay between material choice, manufacturing process, load capacity, finishing, location, volume, and lead time empowers informed decision-making in metal grating procurement. By aligning these elements with project demands, it is possible to secure not only a competitive price but also a product that meets performance expectations and stands the test of time.