In the industrial sector, heavy duty gratings stand as a fundamental element across various applications, providing robust support and efficient drainage. The range of uses and unmatched durability of these gratings make them indispensable in environments demanding superior strength and reliability. This comprehensive exploration of heavy duty gratings delves into the intricate balance of engineering, materials, and design expertise that culminates in their extensive applicability and trustworthiness.
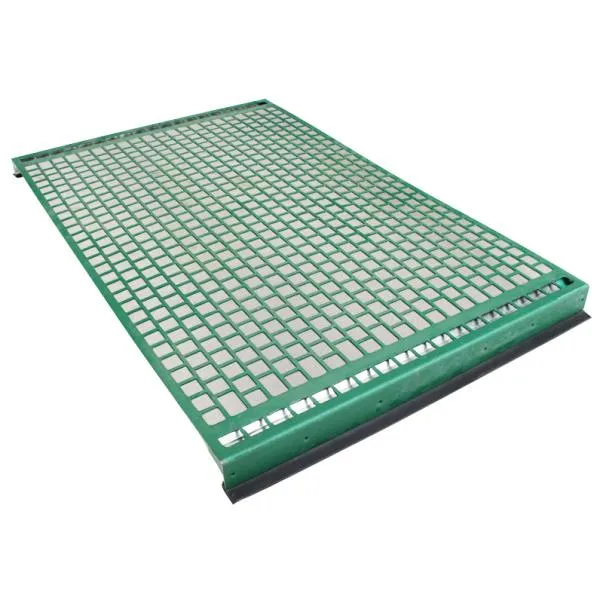
Heavy duty gratings are engineered to serve a dual purpose providing load-bearing capability and ensuring safety. They are an integral part of infrastructure in areas like chemical plants, oil rigs, construction zones, and transportation facilities. Experience from industry leaders illustrates time and again the critical role these gratings play in maintaining operational continuity and safety standards.
A distinctive feature of heavy duty gratings is their construction material. Steel, particularly galvanized and stainless variants, dominate the production due to their higher tensile strength and resistance to environmental stressors. This resistance ensures longevity even in corrosive environments. Manufacturers leverage advanced metallurgical processes to enhance the grain structure of steel, thereby increasing its load-bearing capacity while minimizing weight. The choice of material is also influenced by the specific demands of the application, where factors like chemical exposure and temperature fluctuations are key considerations.
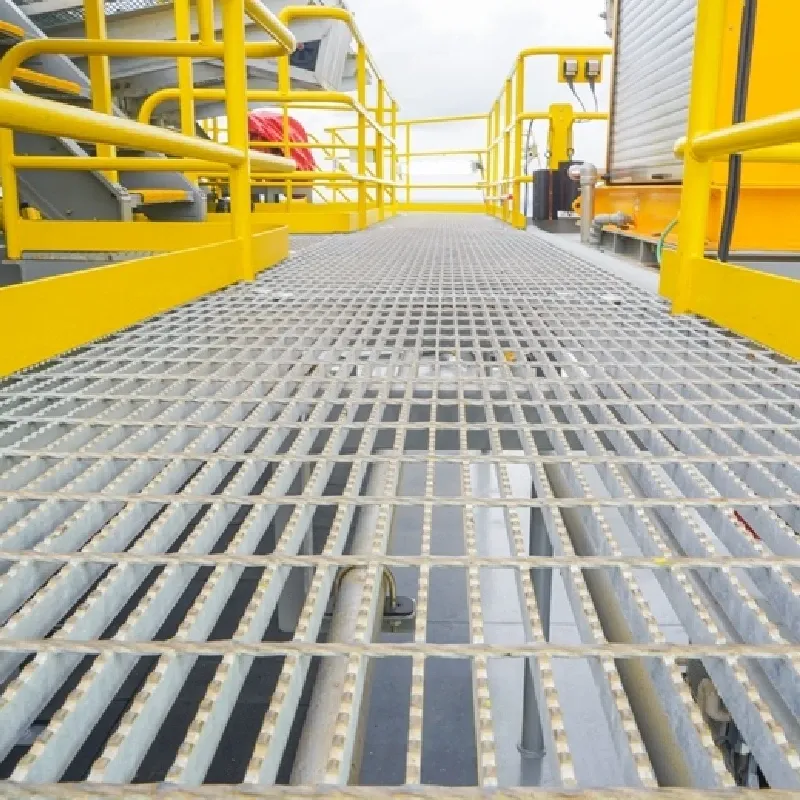
Expertise in the design of heavy duty gratings is paramount to ensuring optimal performance. Engineers meticulously calculate load ratings, factoring in not just static loads but dynamic and impact forces that might occur. The design often features cross bars welded to bearing bars, creating a mesh that distributes weight evenly and reduces the risk of deformation. Tailored grating solutions are custom-designed for specific applications, ensuring that every installation meets stringent safety and design standards.
Furthermore, the authoritative implementation of heavy duty gratings involves compliance with international safety and quality standards such as ISO and ANSI. Industry authorities conduct thorough testing, including load testing and corrosion resistance evaluations, to certify products. Businesses rely on these certifications, knowing that adherence to such standards signifies product reliability and safety.
heavy duty gratings
Trustworthiness in heavy duty gratings stems from both their proven performance history and the continual advances in manufacturing technologies. Innovations such as the development of composite gratings, made from a blend of fiberglass and resin, have expanded applications into environments where metal might not be suitable due to electric conductivity or further corrosive elements. These alternatives offer comparable strength and are particularly beneficial in offshore or wet environments.
From a product lifecycle perspective, heavy duty gratings offer significant economic benefits. Their durability means lower replacement costs and reduced downtime, crucial for sectors where time equates to financial expenditure. Maintenance of these gratings is minimal, typically requiring inspections and minor repairs, while their lifespan can extend for decades with proper care, reinforcing their role as a cost-efficient solution in the greater infrastructure ecosystem.
A case in point of the impact of heavy duty gratings is their use in urban settings. Gratings in drainage systems protect from flooding, maintain hygiene by ensuring proper waste flow, and support the weight of vehicles and pedestrians. The incorporation of anti-slip surfaces enhances pedestrian safety, an essential feature in high-foot traffic areas.
The expertise in deploying heavy duty gratings extends beyond simply installing metal meshes. Professionals assess environmental factors and potential risks before selecting the type of grating. In regions prone to seismic activities, grating systems are integrated with flexible components to absorb energy and prevent structural damage. In contrast, areas with extreme temperatures might require specific coatings that preserve the integrity of the structure.
In conclusion, heavy duty gratings represent a confluence of engineering precision, material science, and design acumen. Their application is a testament to expertise and innovation, providing reliable and versatile solutions across diverse industrial landscapes. With ongoing advancements and adherence to strict standards, these gratings continue to embody trustworthiness and authority, ensuring their position as a pivotal component in modern infrastructure. Businesses and industry leaders rely on them, confident in the products' ability to withstand the test of time and environmental challenges.