Galvanized grating is an essential component in various industrial and architectural applications due to its durability, corrosion resistance, and strength.
Understanding the different sizes and specifications of galvanized grating is crucial for selecting the right product for the intended use. This article delves deep into the nuances of galvanized grating sizes, providing insights grounded in real-world expertise, professional authority, and a commitment to accuracy and reliability.
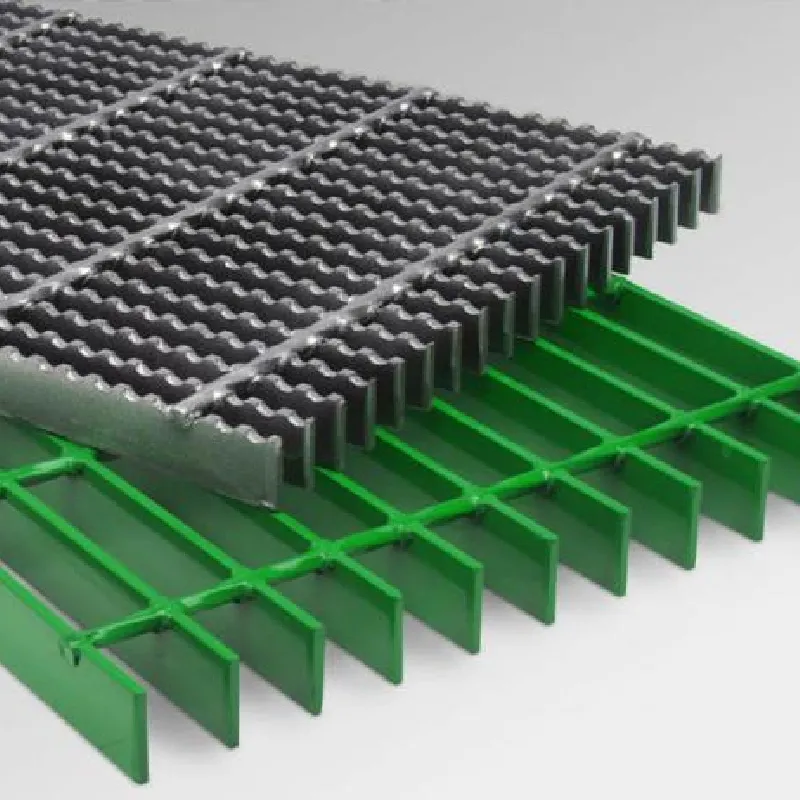
Galvanized grating is primarily made from steel that has been coated in zinc to protect against rust and corrosion, making it a favored choice for both indoor and outdoor applications. The sizes of galvanized grating are determined by several factors, including bar thickness, bar height, and spacing between the bars, each critical to ensure optimal performance in specific settings.
Bar thickness and height are two of the most significant dimensions influencing the strength and load-bearing capacity of grating. Commonly, the bar thickness can range from 3/16 inch to 1/4 inch, while heights can vary from 3/4 inch to 2 inches or more. In industrial environments where heavy machinery or materials will be placed upon the grating, higher bars and greater thickness are often required to withstand significant weight without deformation.

Equally important is the spacing between the bearing bars, which typically ranges from 1 inch to 1 3/16 inches on center. The spacing determines the amount of open space within the grating, influencing everything from drainage capability to safety. For applications requiring maximum drainage, wider spacing is preferred; however, for areas where foot traffic is high, closer spacing provides a flatter, safer walking surface.
It is equally important to consider end-user specifics like slip resistance, which is often achieved by serrated surfaces. Serrated galvanized gratings offer additional grip, reducing the risk of slipping, especially in environments prone to oil or water exposure. A prominent choice for oil rigs or dockyards, this type of grating combines safety with functionality.
Industry standards play a pivotal role in determining the legitimacy and appropriateness of a galvanized grating size for a given application. Standards such as ASTM A123 and ASTM A385 provide guidelines on zinc coating thickness and overall structural integrity, ensuring that each grating product meets the necessary durability and safety benchmarks. Adherence to these standards is non-negotiable for projects that prioritize quality and reliability.
galvanized grating sizes
Additionally, the weight of the grating, often calculated per square foot, is a consideration for logistics and installation. Heavier gratings, while generally more robust, require more support for installation and transportation, impacting the overall project cost and timeline. Lightweight alternatives can, however, present cost-effective solutions in scenarios where maximum load-bearing is not a principal concern.
Custom configurations are an option for unique projects requiring non-standard sizes. Manufacturers often provide design services to tailor bar thickness, height, and spacing to specific engineering requirements. This customization provides flexibility, allowing architects and engineers to achieve aesthetic goals without compromising on performance.
When selecting galvanized grating, it's imperative to consult with industry professionals and trusted manufacturers who provide comprehensive data sheets and certifications. This documentation confirms compliance with relevant standards and ensures confidence in the quality of the material. Partnering with established suppliers safeguards against common pitfalls, such as prematurely failing coatings or structural weaknesses.
It is clear that selecting the right galvanized grating size is not merely a matter of choosing dimensions; it is about understanding the application, comprehending the material's limitations and strengths, and relying on authoritative guidelines for performance. The right choice can enhance project value, ensure longevity, and maintain the safety and functionality of the built environment.
In conclusion, when considering galvanized grating sizes, remember that the expertise lies in a detailed assessment of needs versus specifications. Careful consideration and consultation not only optimize application outcomes but also enhance trust and credibility in the solutions provided. Make informed decisions based on solid expertise, and you will achieve both performance excellence and lasting durability in your projects.