Bar grating weights are crucial when selecting the right grating for industrial, architectural, or commercial projects. With years of expertise in the field, I've observed that understanding how these weights impact both functionality and design is a critical element of successful project execution.
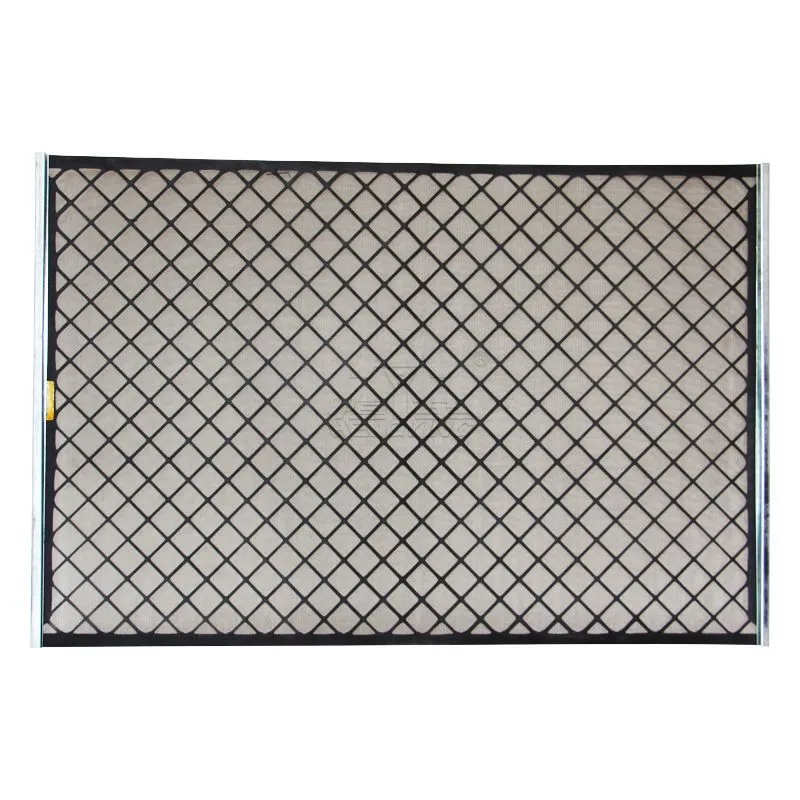
To begin, bar gratings are typically manufactured using materials like carbon steel, stainless steel, or aluminum, each with its unique weight attributes. These materials are chosen based on factors such as load requirements, environmental conditions, and budget considerations. The weight of bar grating directly influences its strength, durability, and ease of installation.
Carbon steel grating is popular for environments where strength is paramount. Due to its weight, it offers superior load-bearing capacity, perfect for situations such as pedestrian footbridges or industrial platforms. However, the heft of carbon steel may demand reinforced support structures, impacting both cost and complexity during installation. It's a common oversight to underestimate this factor, so precision in calculations is essential to optimize both budget and structural integrity.

Stainless steel, on the other hand, brings the advantage of corrosion resistance, making it ideal for environments exposed to moisture or chemicals. Its weight is generally less than carbon steel, reducing installation challenges while sustaining significant strength. In food processing facilities or chemical plants, the slight variance in weight when opting for stainless steel can equate to long-term savings on maintenance and replacements, asserting the importance of material selection in corrosive conditions.
Aluminum gratings, known for their lightweight nature, are advantageous for projects requiring mobility or ease of installment like temporary walkways or exhibition setups. Although aluminum lacks the weight and hence the load capacity of steel gratings, it counters this with versatility. Installers find aluminum preferred for projects where rapid assembly and disassembly are frequent, highlighting its practicality despite lower strength ratings compared to heavier options.
bar grating weights
The method by which these gratings are measured further adds to the complexity of determining suitable bar grating weights. The main metrics include bearing bar size, spacing, and thickness.
A thicker bearing bar directly equates to higher weight but also increased load capacity. On the contrary, wider spacing could reduce weight but limit load-bearing capacity. Therefore, it is imperative to assess project constraints and functional requirements in balancing these variables. Consulting with a structural engineer can significantly aid in achieving the proper configuration that meets specific project demands without overloading the support framework.
Advanced technology and computer-aided design software enable precise calculations and visualizations of how different grating weights affect structural dynamics. I've seen project managers leverage these tools to simulate stress and load tests, which can provide insights into long-term performance and feasibility. Embracing technology not only streamlines the decision-making process but increases confidence in compliance with safety and industry standards.
Trustworthy sourcing also plays a pivotal role. Ensuring that bar grating is purchased from reputable manufacturers guarantees adherence to global quality standards, which influences both weight consistency and structural reliability. Inadequate quality control can result in variations in weight and strength, leading to project delays or failures.
Concluding, while bar grating weight is just one of many considerations in your selection process, its significance cannot be overshadowed. The interplay between material choice, configuration, and precise engineering consultation inform the selection of the ideal grating. By giving due diligence to these factors, project outcomes are not just successful but exemplary.