Steel grating galvanizing is a pivotal process that manufacturers prioritize to ensure durability, resistance, and overall quality of the steel grating products. Drawing from years of industry expertise and real-world experience, we delve into the profound benefits and specific technical attributes of galvanizing, establishing why this process remains a cornerstone in the production of steel gratings.
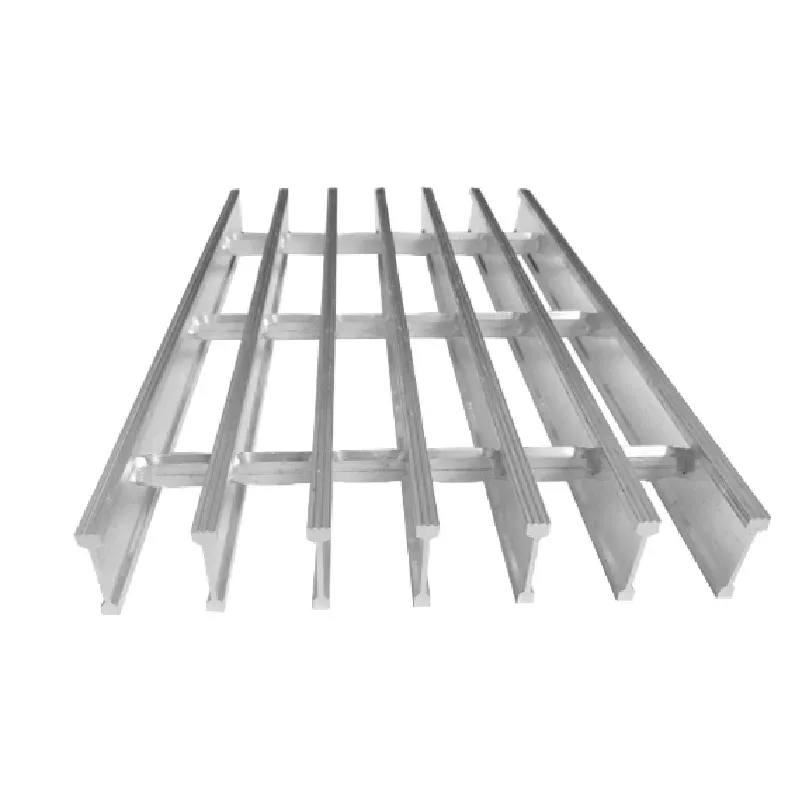
Galvanization, involving the coating of steel or iron with a layer of zinc, primarily functions as a protective barrier. This zinc layer is crucial as it offers cathodic protection. When the steel grating surfaces encounter corrosive elements, the zinc corrodes preferentially, thereby preserving the underlying material. This safeguard is particularly essential in environments where the grating is exposed to moisture, chemicals, or physical wear, ensuring longevity and reducing maintenance costs.
In practical terms, a hot-dip galvanizing process is most frequently implemented, wherein the steel grating is immersed in a bath of molten zinc. Expertise highlights that this method yields a coating that is robust and uniform, covering even the most intricate parts of the grating structure. This uniformly applied coat is instrumental in enhancing the steel grating’s wear-resistance, making it ideal for industrial applications.
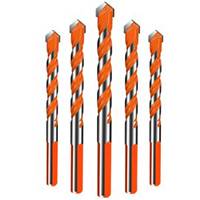
Steel gratings, often deployed in factories, walkways, and drainage covers, are subject to heavy loads and high foot traffic. The galvanized layer not only prevents rust but also reinforces the structural integrity of the grating. Experts assert that galvanized gratings withstand significant mechanical stresses and offer anti-slip properties even in adverse weather conditions. This reliability underscores their use in safety-critical environments.
Furthermore, galvanization is recognized for its cost-effectiveness. While the initial application might increase production costs marginally, the long-term savings from reduced rust repairs and replacements are considerable. Professionals in the construction and industrial domain often prefer galvanized steel gratings for projects that demand sustainability and durability.
steel grating galvanis
Trust in galvanized steel grating also stems from rigorous quality standards. Compliance with international standards such as ASTM A123/A123M assures stakeholders of the product’s premium quality. Manufacturers holding these certifications are regarded as authoritative entities, providing further assurance to consumers regarding product performance.
Aligning with environmental safety, the galvanization process has evolved to reduce waste and utilize resources efficiently. Advanced techniques and improvements in the galvanizing process have curtailed zinc consumption, ensuring that production is eco-friendly, which is a critical consideration for environmentally conscious developers and engineers.
Delving into user experience, feedback from end-users consistently highlights the resilience and minimal maintenance needs of galvanized steel gratings. Facility managers and site engineers appreciate their aesthetic appeal and the peace of mind that comes with selecting a product designed to resist extreme conditions. Such insights from real-world applications testify to their effectiveness and trustworthiness, contributing to their widespread adoption.
In synthesis, galvanized steel grating stands as a product marked by remarkable durability, unparalleled protection, and substantial economic advantages. It is a trusted choice for many sectors due to its proven performance in combating corrosion and withstanding heavy use. The amalgamation of expert technology, adherence to strict standards, and environmental consideration places steel grating galvanizing at the forefront of material innovation, securing its place as a vital component in contemporary infrastructure and industrial projects.