For anyone invested in the world of oil exploration or similarly demanding environmental fields, securing the right equipment is paramount. A vital component among such equipment is the shaker screen, an essential part of the drilling fluid process used to separate different sizes of material. When considering shaker screens for sale, it's crucial to make informed choices based on authentic experiences, specialized knowledge, authoritative guidance, and trustworthiness.
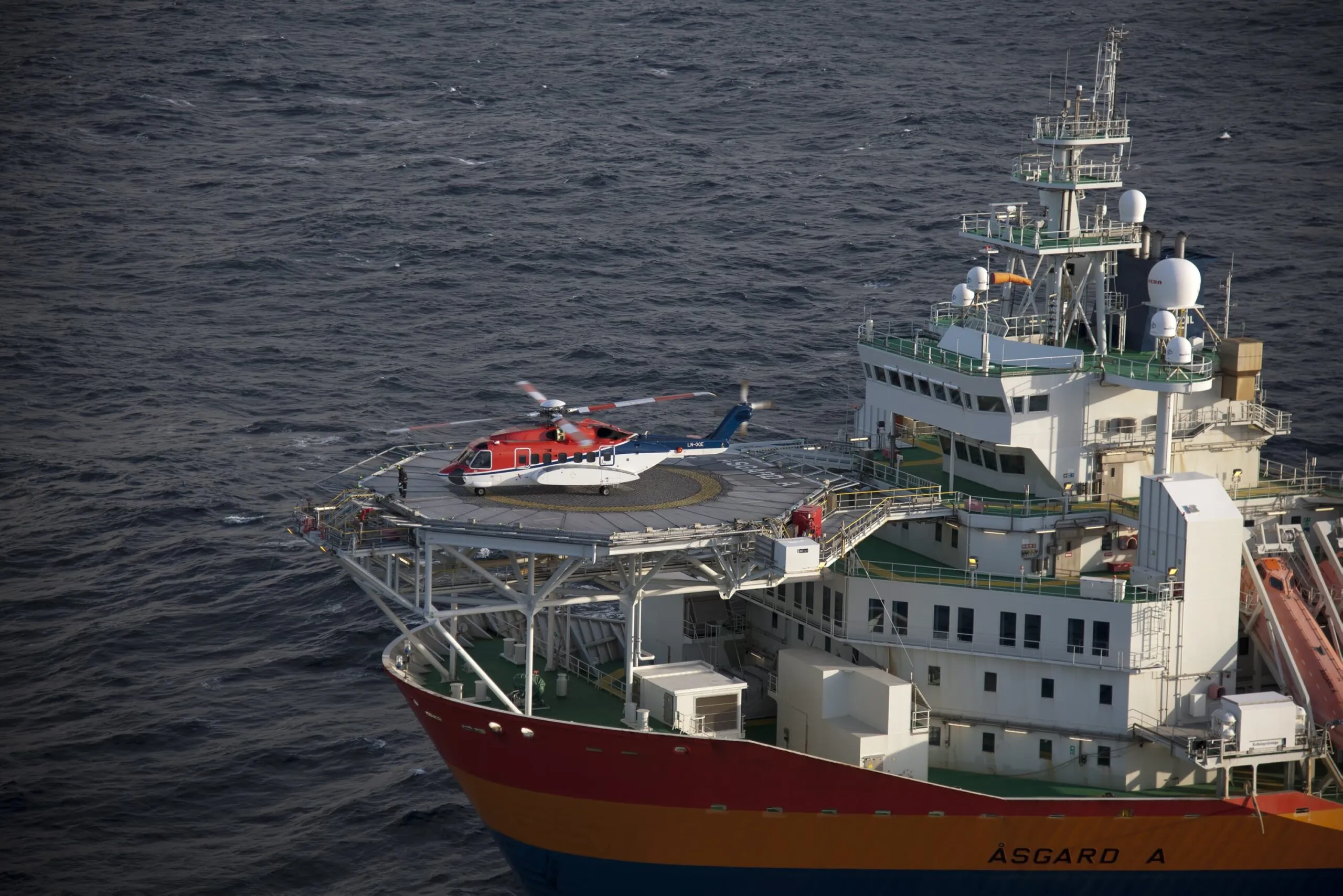
An industry favorite for its efficiency and reliability, the shaker screen has often been likened to the unsung hero of drilling operations. When optimized, it significantly enhances the drilling fluid management process, ensuring a smooth and streamlined task flow. From stopping unnecessary downtimes due to clogging to maximizing the life cycle of drilling fluids, a well-chosen shaker screen can be the difference between average and outstanding project metrics.
The expertise required in selecting a shaker screen begins with understanding the types of screens available on the market. Primarily, these screens are categorized based on mesh size, material, and the unique system designs from different manufacturers. Mesh size determines the size of particles that can be separated; smaller mesh numbers correlate with larger openings, allowing larger particles to pass through. Such insight is crucial for selecting a screen that aligns with the specific demands of the project in question.
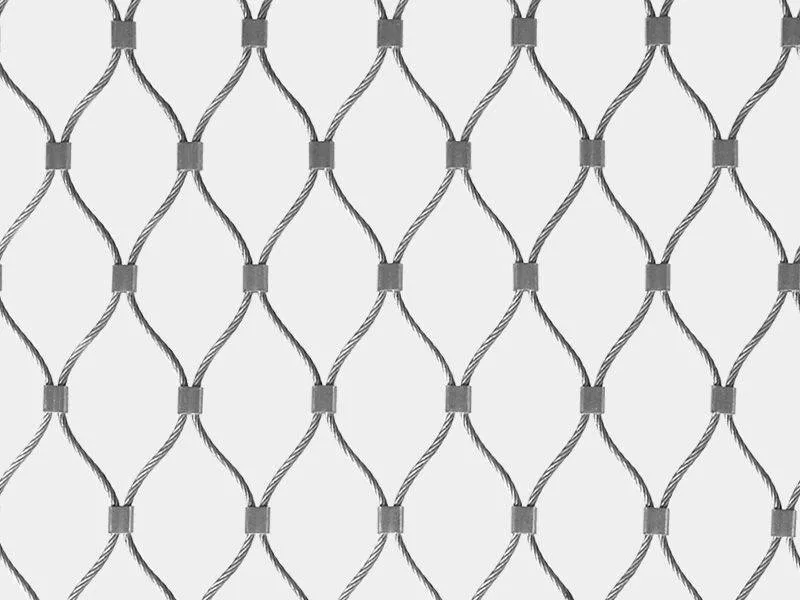
Material selection is another fundamental aspect with options generally encompassing stainless steel and composite materials. Stainless steel screens, known for their durability and heat resistance, are often recommended for operations that entail severe working conditions. On the other hand, composite screens, often lighter and potentially more cost-effective, provide flexibility and ease of installation. A professional with in-depth knowledge of the operation can discern which material aligns with the particular environmental and operational challenges faced.
Authority in the field of shaker screens comes from manufacturers who have stood the test of time and continually evolve their product lines to meet modern challenges. Established brands tend to offer not only product quality but also comprehensive support services ranging from installation guidance to maintenance tips. An array of support services can be an essential factor when purchasing, as it further validates the company's commitment to the customer’s success and operational efficiency.
shaker screen for sale
Trust in the purchase process is tied closely to the authenticity of the product and vendor reliability. Ensuring that screens are sourced from reputable sellers who offer warranties and have clear return policies establishes a safeguard against potential operational issues. Customer reviews and testimonials play a pivotal role here; real-world accounts provide a lens into product performance and vendor reliability.
Once the proper shaker screen is chosen, integrating it into the existing system requires precision and understanding of its operational impact. Correct installation and regular maintenance can prolong the screen's life and maintain its effectiveness. Industry professionals often liaise with technical teams to finetune the screen’s performance depending on real-time project needs and environmental changes.
The right shaker screen does more than filter drilling fluids effectively—it supports cost savings and enhances operational safety. By preventing equipment downtime and reducing fluid loss, a well-appointed screen can indeed lower overall project costs and improve productivity.
Navigating the market with a focus on experience, expertise, authority, and trust will lead to not only the right purchase but will directly impact project outcomes positively. Consequently, investing time and resources to understand the intricacies involved in shaker screen selection is not just recommended but essential. This conscientious approach ultimately ensures that the procurement of shaker screens aligns perfectly with the operational goals and environmental demands of any drilling project.