Serrated grating weight is an aspect that often goes unnoticed when selecting the ideal material for industrial and commercial applications, yet it plays a crucial role in both performance and safety. With decades of industrial expertise, understanding the unique qualities of serrated grating weight can provide an edge in decision-making, ensuring that projects meet both functional and safety standards while optimizing costs.
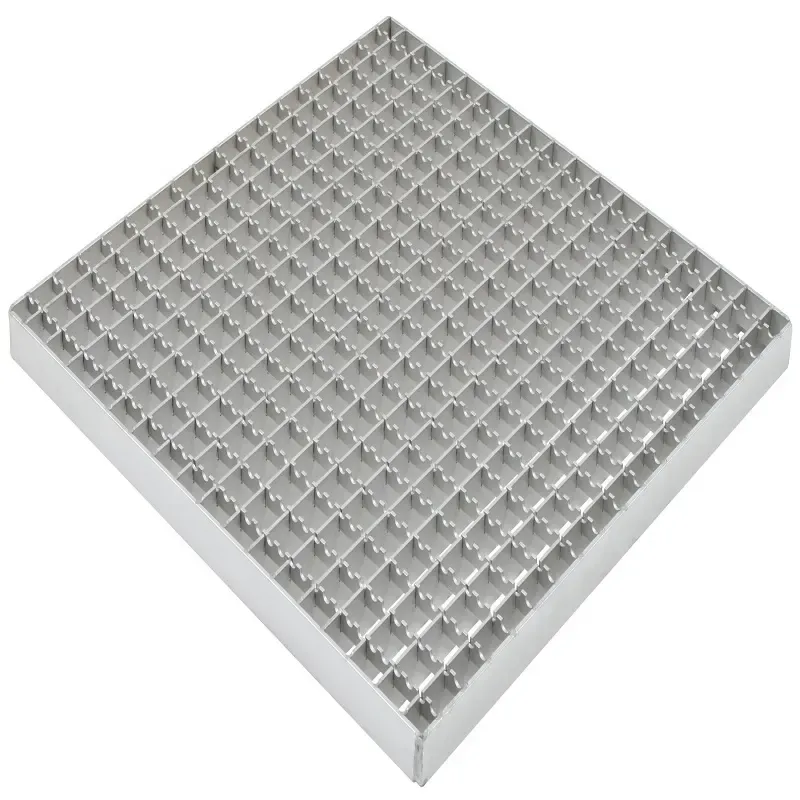
Serrated grating is a preferred choice in environments where slip resistance is paramount. The serrated edges dramatically reduce the risk of slipping, making it ideal for platforms, walkways, and stair treads, particularly in industrial settings that handle liquids or other slippery substances.
The weight of serrated grating is fundamentally influenced by the materials used and the specific design patterns. Common materials include steel, aluminum, and fiberglass, each offering distinct benefits. Steel grating, often lauded for its strength and durability, is heavier, which can be both a benefit and a drawback depending on the project requirements. On one hand, its weight contributes to stability and resistance to heavy loads, crucial for areas with high traffic or that require equipment support. On the other hand, installation requires more effort, possibly influencing labor costs and duration.
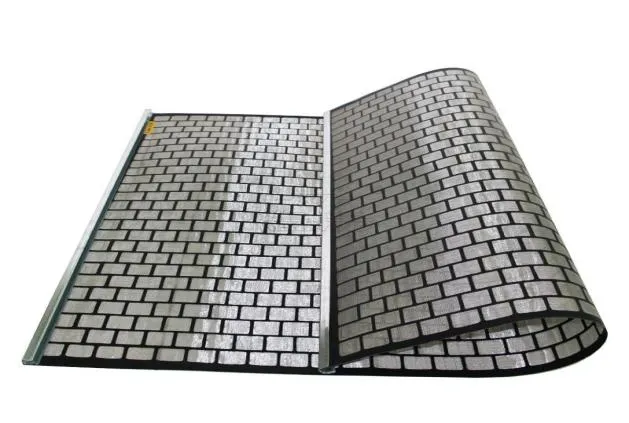
Aluminum serrated grating offers a lighter alternative without significantly compromising on strength. This makes it a favorable option for projects where ease of installation and maintenance are prioritized. Aluminum's resistance to corrosion makes it particularly suitable for outdoor environments or those exposed to harsh weather conditions. However, while lighter, aluminum serrated grating may not support as much weight as its steel counterpart, which is an important consideration during the planning phase.
serrated grating weight
Fiberglass serrated grating stands out due to its exceptionally lightweight and non-corrosive properties. It's often the go-to for chemical plants or aquatic applications where metal gratings would fail due to rust or chemical reaction. While its lightweight nature facilitates easy installation and reduces transportation costs, it is important to note that fiberglass may not offer the same load-bearing capacity as metal options. However, in environments where safety from electric conductivity is a concern, fiberglass is unmatched.
When evaluating serrated grating for a project, it is crucial to consider the weight in relation to its application. Load rating, environmental conditions, and maintenance needs are all factors that must be assessed. A thorough understanding of these aspects enhances the credibility and trustworthiness in advising and selecting the most fitting serrated grating type.
The expertise involved in selecting the proper serrated grating also extends to compliance with safety standards. Ensuring that the weight of the grating aligns with industry regulations is not just a matter of legal adherence but also of safeguarding lives and infrastructure. Consulting with engineers and safety experts during the planning phase can greatly enhance the author's expertise and authoritativeness in this field, reinforcing trust from stakeholders.
Overall, the weight of serrated grating is a pivotal element in the selection process that demands careful balance. It requires an in-depth understanding of material science, structural engineering, and environmental challenges. By coupling these insights with real-world experiences and expert evaluations, decision-makers can confidently select serrated grating that optimizes performance, safety, and cost-efficiency for any application.