Galvanized grating, an essential component in a range of industrial and commercial applications, comes in various sizes tailored to meet diverse requirements. When selecting the best size for a project, it's crucial to consider factors such as load requirements, environment, and specific application needs. Let's delve into the intricacies of galvanized grating sizes to understand their significance and guide you in making informed choices.
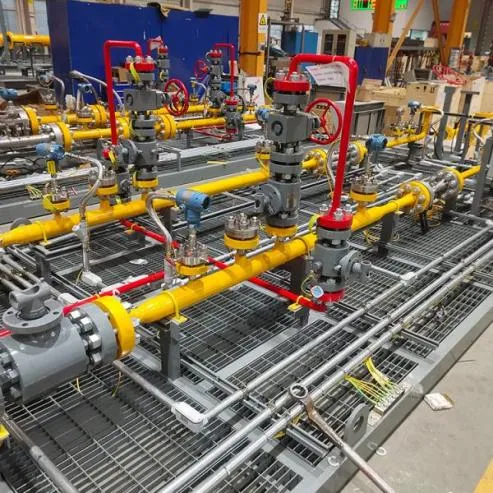
Galvanized grating is commonly used in industries such as construction, manufacturing, and infrastructure for flooring, walkways, stair treads, and drainage covers due to its strength, durability, and resistance to corrosion. The process of galvanization involves coating steel or iron with a protective layer of zinc, which enhances its longevity and performance in harsh environments.
The sizes of galvanized grating are determined by several factors, including bar size, spacing, and panel dimensions. These factors not only impact the grating's structural integrity but also its ability to perform in specific environments.
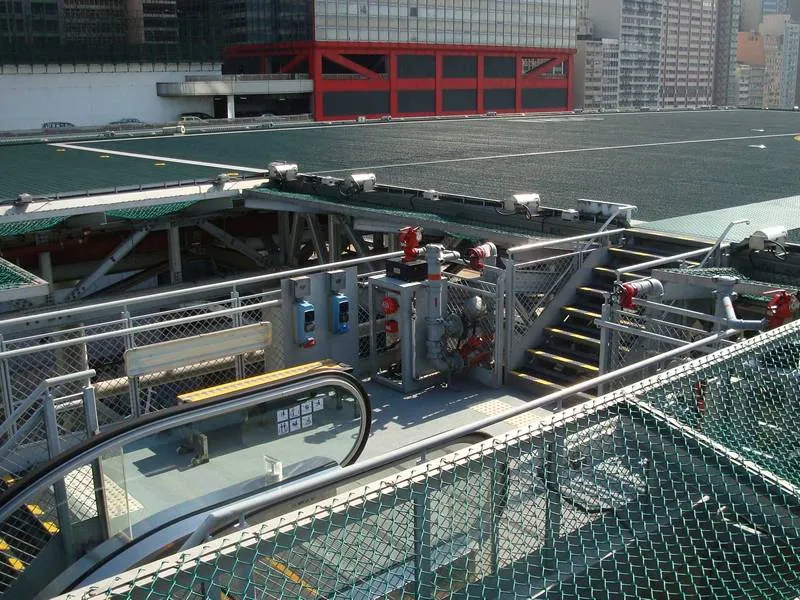
Bar size, or thickness, plays a pivotal role in the grating's load-bearing capacity. Common bar sizes range from 3/4 inch to 2 inches, with thicker bars providing superior strength. For applications that demand high load capacity, such as industrial floors or vehicular pathways, a thicker bar size is advisable.
Spacing, the distance between each bearing bar, influences both the grating's strength and its safety features. Standard spacing configurations include 19-w-4 (19/16” on center) and 15-w-2 (15/16” on center). The spacing choice should take into account both the load specifications and the safety regulations pertinent to the project. Closer spacing may be required for areas where foot traffic is high, reducing the risk of trips or falls.
Panel dimensions, which can vary significantly, are often customized to suit the project. Standard panel sizes typically range from 24 inches by 96 inches, although custom sizes can be manufactured to fit non-standard floor layouts or unique structural designs. The right panel size minimizes waste and reduces installation time, adding both economic and practical value to a project.
galvanized grating sizes
Selecting the correct galvanized grating size involves balancing practical requirements with regulatory compliance. The American Welding Society (AWS) and the Occupational Safety and Health Administration (OSHA) provide guidelines that govern the safe use of grating in various settings. Ensuring compliance with these standards safeguards against potential liabilities and enhances the project's overall integrity.
In real-world applications, businesses often consult with grating specialists or engineers to determine the best size and configuration for their specific needs. These experts consider factors such as anticipated loads, environmental conditions (e.g., exposure to chemicals or weather elements), and project specifications to recommend optimal solutions.
In industries where grating is employed in highly corrosive or extreme temperature environments, the combination of galvanization with additional coatings or treatments may be necessary to extend the material's lifespan further. For instance, when used in coastal or marine applications, a heavier zinc coating might be considered to withstand the increased threat of corrosion.
Economic factors also influence grating size decisions. Although larger sizes or custom configurations may incur higher initial costs, the long-term benefits of durability, compliance, and reduced maintenance can offer substantial financial advantages over time. Organizations often perform a cost-benefit analysis to weigh the initial investment against the potential savings on operational disruptions, injury claims, or frequent replacement costs.
Finally, the successful selection and installation of galvanized grating sizes depend on meticulous planning and a thorough understanding of the specific use case. By leveraging professional expertise and maintaining a clear focus on both the technical and compliance aspects, organizations can ensure that their choice of grating will meet functional demands while also delivering on durability and safety expectations.
In summary, navigating the complexities of galvanized grating sizes requires a blend of engineering insight, regulatory awareness, and economic consideration. With the right approach, galvanized gratings not only meet the immediate project needs but also contribute to a safe, efficient, and cost-effective solution in the long run.