In the dynamic world of construction and industrial design, the role of aluminum grating often extends beyond structural support, becoming an integral component in applications demanding durability and flexibility. Understanding the nuances of aluminum grating pricing requires an in-depth look into its production, applications, and market demand, all while fostering the principles of Experience, Expertise, Authoritativeness, and Trustworthiness.
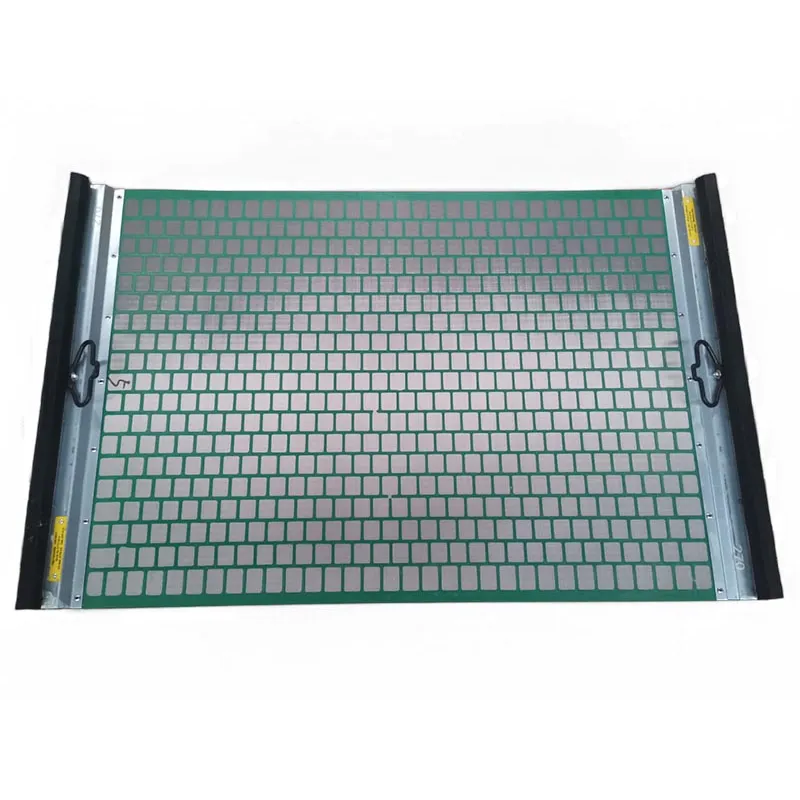
Aluminum grating, renowned for its lightweight yet robust nature, is a staple in sectors requiring high strength without the burden of added weight. Its applications are diverse—spanning from industrial flooring, platforms, and walkways to ventilation and machinery safety surrounds. The price of aluminum grating is inherently tied to several critical factors ensuring that buyers receive quality proportional to their investment.
Firstly, material quality is paramount.
The purity of the aluminum used directly influences the price. High purity aluminum grating tends to be more costly due to its enhanced features such as greater corrosion resistance and a higher degree of adaptability under different environmental conditions. Industrial experts underline the necessity of sourcing from suppliers who prioritize quality through continuous testing and certification, which not only assures longevity but also aligns with international safety standards.
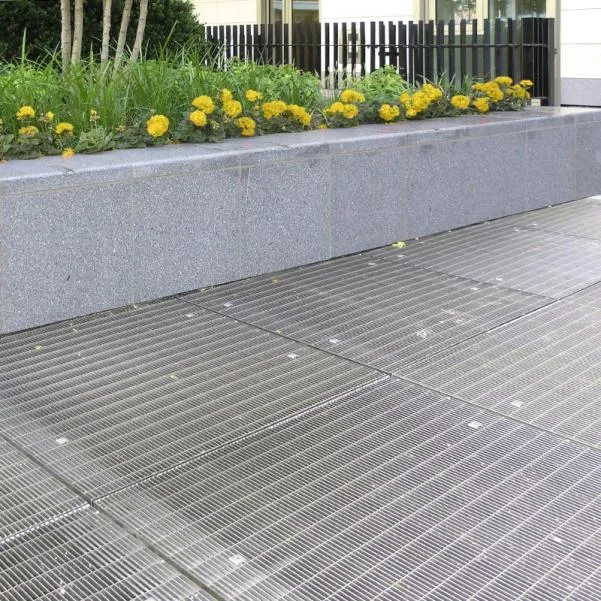
The manufacturing process substantially impacts the pricing framework. Techniques such as welded and pressure-locked grating affect not only the strength and application of the products but also their cost. Welded grating typically involves a more labor-intensive process, ensuring a robust bond between joints, thus commanding a higher price. In contrast, pressure-locked grating, preferred for its aesthetic appeal due to its clean, uniform look, might present a more economical choice while maintaining structural integrity.
aluminum grating price
Moreover, customization plays a significant role. As industries demand solutions tailored to specific requirements, the capacity to customize dimensions, load-bearing demands, and surface treatments influences the overall cost. Custom solutions, though potentially pricier, provide exact matches to project specifications, thereby mitigating future costs associated with retrofitting or replacements. Engaging with manufacturers who demonstrate expertise in providing bespoke solutions can ensure precise alignment with project goals, balancing cost and functionality seamlessly.
The economic dynamics, including market demand and the cost of raw materials, inevitably sway aluminum grating prices. Recent trends suggest a shift towards sustainability, pushing industries to explore eco-friendly options, including recycled aluminum, which can present a cost-effective yet environmentally responsible alternative. Additionally, geopolitical factors and fluctuations in global trade policies can impact the availability and pricing of both raw and finished materials.
To navigate the complexities of aluminum grating pricing, industry leaders emphasize building relationships with reputable suppliers who provide transparent pricing models and detailed product specifications. This approach roots the purchasing decision in trustworthy information, ensuring investments are well-placed and project timelines remain unaffected by unforeseen discrepancies in product performance.
In conclusion, understanding the multifaceted layers contributing to aluminum grating prices forms the bedrock of informed decision-making. By prioritizing quality, considering production processes, embracing customization, and maintaining a vigilant watch over market trends and economic factors, practitioners can confidently secure aluminum grating solutions that both meet budgetary constraints and elevate project outcomes. Through a commitment to these principles, businesses not only enhance project success but also reinforce their reputation for reliability and expertise in the competitive market.