Aluminum bar grating stands as an indispensable solution in various industrial and architectural applications. Its popularity stems from its exceptional strength-to-weight ratio, making it a prime choice where both durability and lightweight properties are paramount. When calculating the weight of aluminum bar grating, several factors come into play, influencing both performance and installation. A deeper understanding of these aspects not only assists in precise weight estimation but also optimizes structural planning and efficiency.
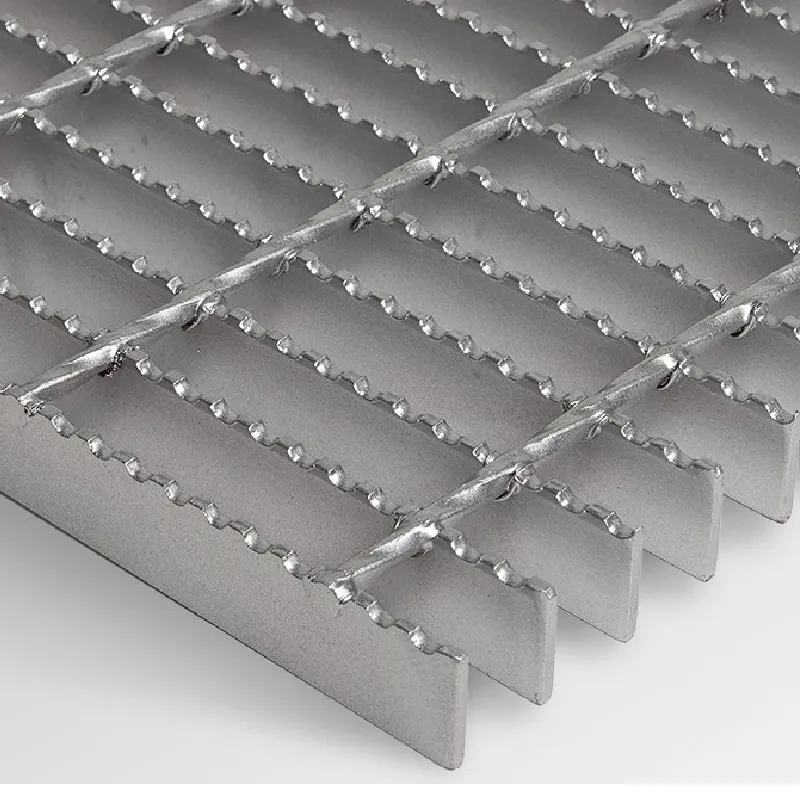
Firstly,
the specific alloy of aluminum used in bar grating significantly affects its weight. Commonly used alloys such as 6061-T6 or 6063-T6 are renowned for their high strength and corrosion resistance. The specific properties of these alloys enable them to provide robust performance even in harsh environments, although they might slightly differ in weight due to variations in their elemental compositions. For example, 6061-T6, with its balance of strength and workability, is often preferred in load-bearing scenarios, whereas 6063-T6’s excellent extrusion characteristics make it ideal for custom designs.
The dimensions of the grating, including the bearing bar and cross bar size, play a critical role in determining the final weight. Bearing bars are the primary load-bearing components in the grating, typically available in varying depths and thicknesses to accommodate different load requirements. A deeper bar provides greater load capacity but also increases the weight per square foot of the grating. Cross bars, while less critical in terms of load bearing, contribute to the overall structural rigidity and influence weight. Therefore, selecting the optimal configuration requires a careful balance between application needs and weight considerations.
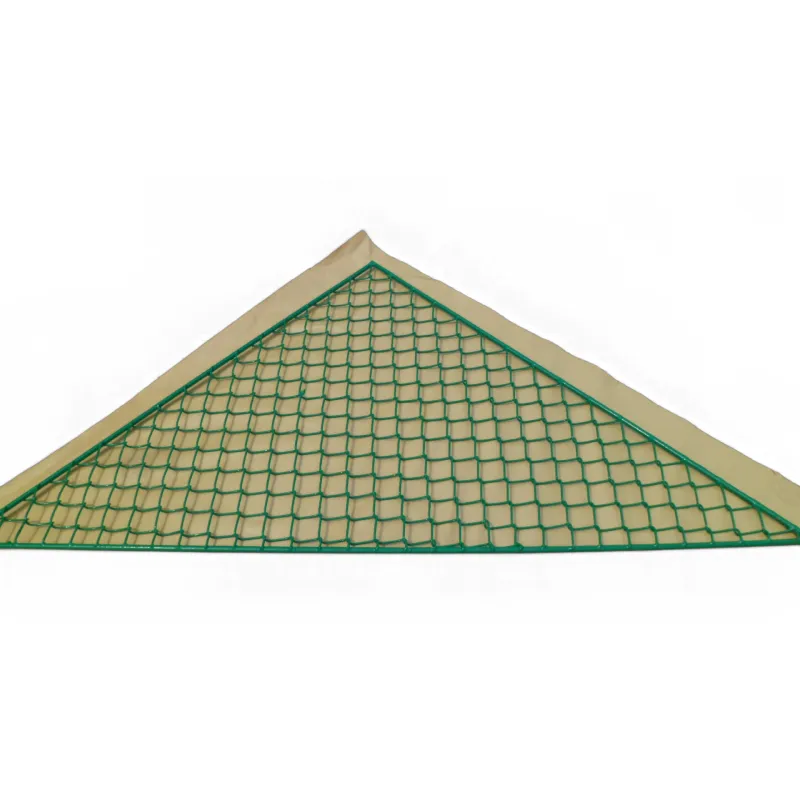
Another vital component is the spacing of the bars, both bearing and cross. Standard spacing options include close-mesh for applications requiring smaller openings and open-mesh for environments where fluid or debris passage is necessary. Close-mesh designs naturally result in a heavier grating solution due to the increased number of bars, whereas open-mesh designs offer weight savings at the cost of reduced load distribution.
The method of grating fabrication—either through welding or swaging—also impacts the weight. Welded bar grating is typically heavier due to the additional material used in the welding process, which creates a permanent bond between bars. Conversely, swaged grating, which employs a mechanical process to bond the bars, can be lighter, making it an attractive option for installations where ease of handling is a priority.
aluminum bar grating weight
Surface treatment of the aluminum grating is another pivotal factor. While untreated grating offers the lowest weight, powder coating or anodizing provides additional corrosion resistance at a marginal weight increase. Such coatings are crucial for prolonging the lifespan of the grating in corrosive environments, justifying the slight addition in weight.
Understanding these variables aids in calculating the precise weight of aluminum bar grating for any given project. When undertaking structural planning, it’s advisable to consult with suppliers and use weight calculators that account for all design specifications. Doing so ensures that the chosen grating not only fulfills the functional requirements but also aligns with logistical preferences, such as transportation and installation ease.
Ultimately, the lightweight attributes of aluminum bar grating offer ample opportunities for innovation across industries. Its ability to maintain structural integrity while reducing overall weight translates into significant cost savings during both construction and lifetime maintenance. Moreover, leveraging advanced manufacturing techniques and materials science continues to improve the efficacy and sustainability of these solutions, reinforcing aluminum bar grating as a top contender in modern engineering projects.
As advancements in material technology evolve, aluminum bar grating remains a versatile and adaptable solution, ideal for a myriad of applications where weight efficiency, strength, and durability are non-negotiable.